MOV SMD Features
In the battle against voltage transients—such as lightning surges, electrostatic discharge (ESD), and switching noise—varistors act as critical “electronic safety valves.” When a voltage spike occurs, the varistor instantly switches from high resistance to low resistance, shunting dangerous energy to ground and protecting sensitive downstream circuits.
As electronic devices continue to shrink and surface-mount technology (SMT) becomes the manufacturing standard, varistors have evolved from traditional radial leaded types to surface-mount (SMD) solutions. But what are the real differences between the two? And how should engineers make the right choice? Boarden provides a clear comparison to help guide your selection.
1. Form Factor & Construction
Radial Leaded Varistor
- Appearance: Typically round or disc-shaped ceramic body with two metal leads.
- Mounting: Requires through-hole insertion and wave or manual soldering, followed by lead trimming.
- Internal Structure: Sintered zinc oxide (ZnO) ceramic disc with electrodes on both sides.
SMD Varistor
- Appearance: Rectangular shape with metallized terminals on the bottom.
- Mounting: Compatible with SMT processes—automated placement and reflow soldering, no leads or trimming required.
- Types:
- MLV (Multilayer Varistor): Resembles MLCCs, built from alternating ZnO-based ceramic layers and electrodes, sintered into a monolithic chip. Boarden include 0402, 0603, 0805, 1206, 1210, and 1812.
- Epoxy Molded/Chip Type: Traditional MOV chips encapsulated in plastic packages (e.g., 3025, 4032), also with metallized bottom terminals. Larger than MLV, but smaller than radial types.
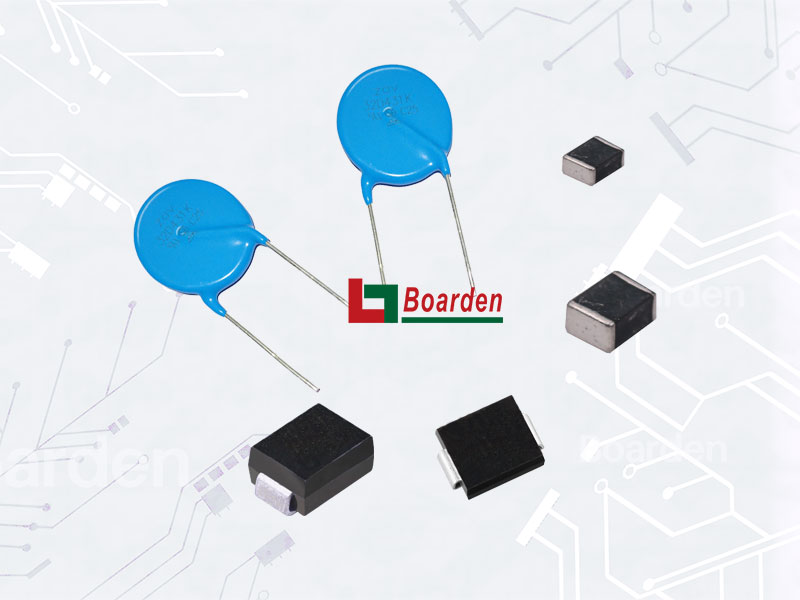
2. Performance Comparison
Feature | Radial Varistor (MOV) | MLV SMD Varistor | Epoxy Molded SMD Varistor |
---|---|---|---|
Key Advantages | • High surge current capacity• Wide voltage range (tens to 1000+ V)• Cost-effective for high power | • Ultra-small size• Fastest response (<1ns)• Ideal for ESD protection• SMT compatible | • SMT compatible• Close to radial MOV performance• Compact size• Fast response, low clamping voltage |
Limitations | • Bulky• Manual soldering• Not suitable for high-density PCBs | • Lower surge capacity• Typically lower voltage rating | • Fewer models (currently)• Not ideal for extreme surge or high-voltage applications |
Target Protection | High-energy surges (e.g. lightning) | Fast transients (ESD, EFT) | Moderate surge, switch spikes, light surge/lightning |
Production Fit | Incompatible with full SMT automation | Fully SMT-compatible | Fully SMT-compatible |
Certifications | UL, TUV, CQC | UL, TUV, CQC | UL, TUV, CQC |
Highlights:
- Surge Capacity: Radial ≈ Molded SMD > MLV
- Response Speed: MLV <1ns > Molded > Radial
- SMT Compatibility: Strong advantage for both MLV and molded SMD types—ideal for automated production lines.
3. Application Scenarios
Radial MOV Applications:
- AC mains input of appliances, industrial equipment, power adapters, UPS
- High-power LED driver input/output
- Main power protection in industrial control boards
- Non-SMT production lines or cost-sensitive, space-insensitive applications
SMD Varistor (MLV & Molded) Applications:
- LED driver input/output (increasingly replacing radial MOVs)
- Smart home controllers and port protection
- Internal protection for chargers, power adapters (DC side)
- White goods control boards
- USB PD ports, DC jacks for primary or secondary surge protection
- High-speed data lines (USB, HDMI, Ethernet) — MLV recommended
- IC I/O pin ESD protection
- DC-DC output EFT suppression
- Automotive low-voltage protection (MLV with AEC-Q200 rating)
- Any compact SMT product requiring board-level surge protection
4. Selection Guidelines
Choose based on the following criteria:
- Protection Location & Surge Type:
- AC input / lightning risk → Radial or high-performance molded SMD
- DC input / secondary power → Molded SMD
- Data/signal lines → MLV preferred
- Surge Energy / Current: High surge → Radial or molded SMD; Low surge or ESD → MLV
- Operating Voltage: High voltage → Radial; Low-to-mid voltage → SMD options
- PCB Space Constraints: Tight space → MLV; Moderate → Molded; Ample → Radial
- Production Method: SMT line → SMD (MLV or molded); Manual/wave soldering → Radial
- Cost Consideration: Factor in not just part cost, but also assembly efficiency. SMT is more scalable and cost-efficient.
Final Thoughts: Tailored Protection for Diverse Needs
Radial and SMD varistors are not direct replacements—they serve distinct purposes across performance, size, cost, and manufacturing compatibility.
- Radial MOVs remain essential in high-surge, high-voltage, or non-SMT applications.
- MLV SMD varistors dominate in high-speed signal protection due to their miniature size and ultra-fast response.
- Molded SMD varistors strike a balance: they offer MOV-like performance while supporting automated SMT assembly—ideal for lighting, smart home, power adapters, and general-purpose power line protection.
✅ The key is to match the varistor type to your circuit’s protection need, surge profile, voltage range, and production setup.
Boarden offers a full line of varistor solutions, including radial MOVs, high-energy MLV (CMS series), and molded SMD varistors—all UL/TUV/CQC certified. We help customers transition smoothly from through-hole to surface-mount protection and support optimized selection across diverse applications.
📩 Need support or samples? Contact Boarden to join our engineer community for technical exchange and application-specific recommendations.